Floating foundation slabs (concrete)
Mini piles are much less cumbersome to transport and install than conventional sheet piles which require specialized machinery, cranes, and temporary supports (shoring). What is mini piling? Mini piling is the installation of pre-manufactured steel or concrete piles, typically 70 cm in length, 25 cm wide and varying in height depending on the surface water level. They are installed below ground at construction sites avoiding the need for heavy equipment. The low-cost but durable design means they can be easily handled by one man without the use of cranes or drill rigs.
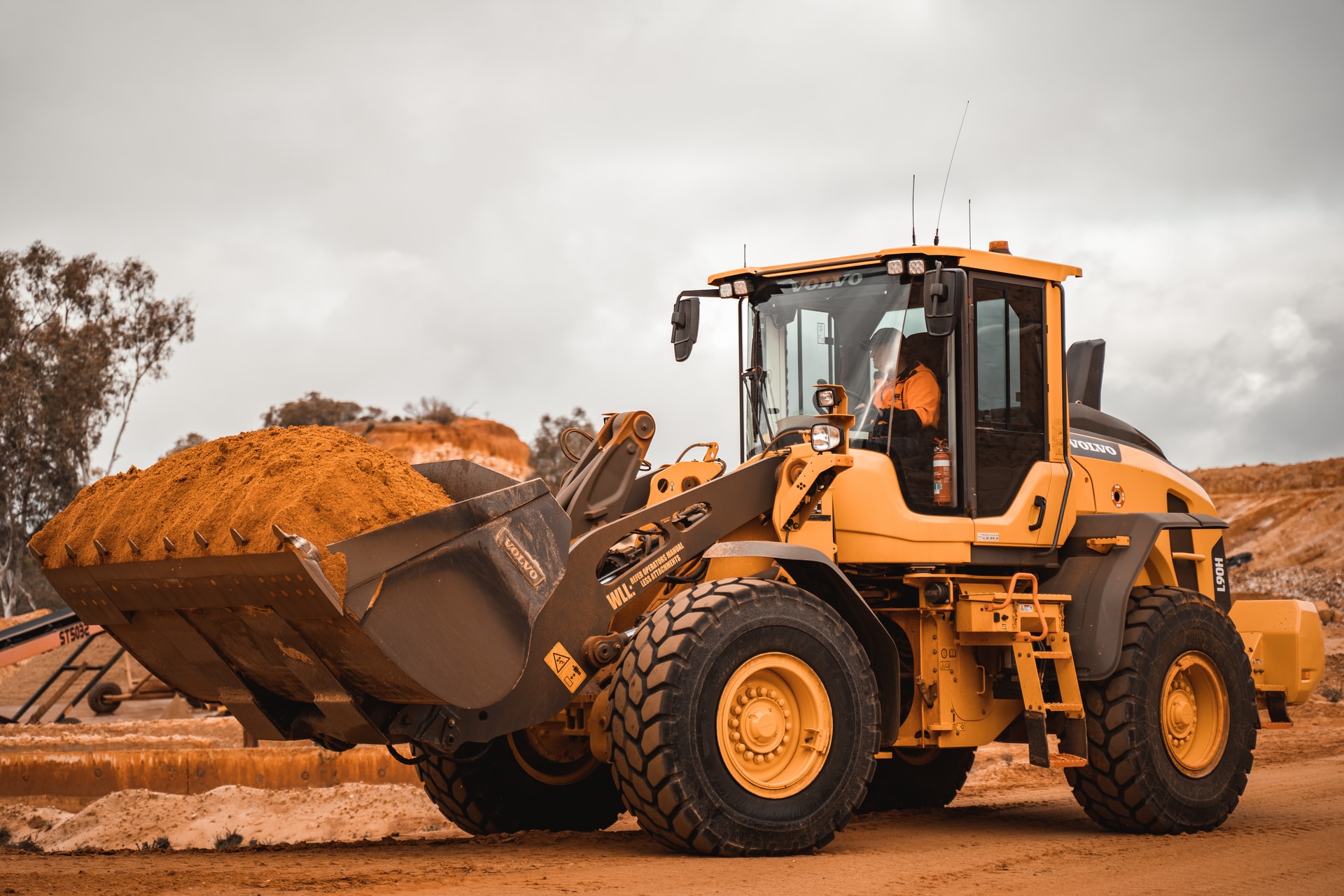
Mini piling techniques
Mini piling techniques
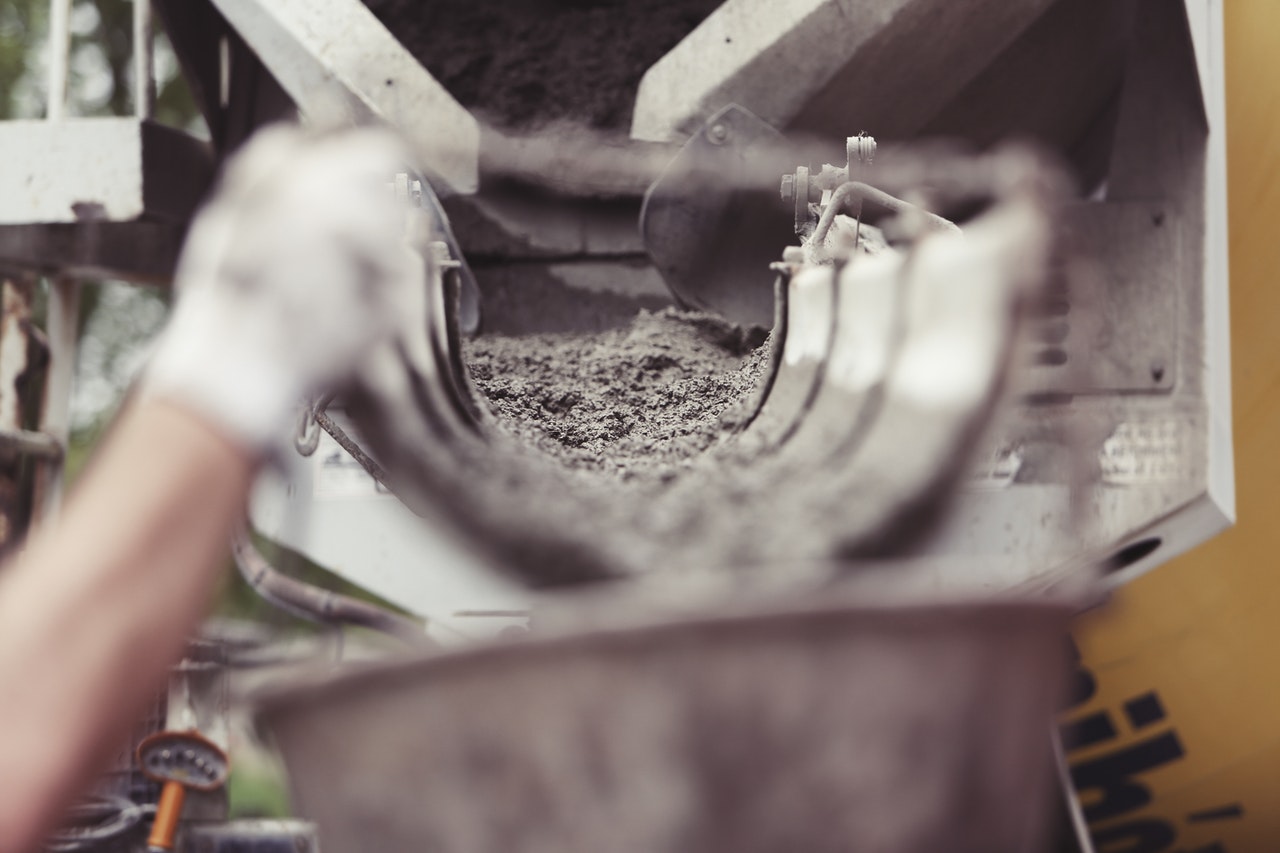
Machine Mini Piling
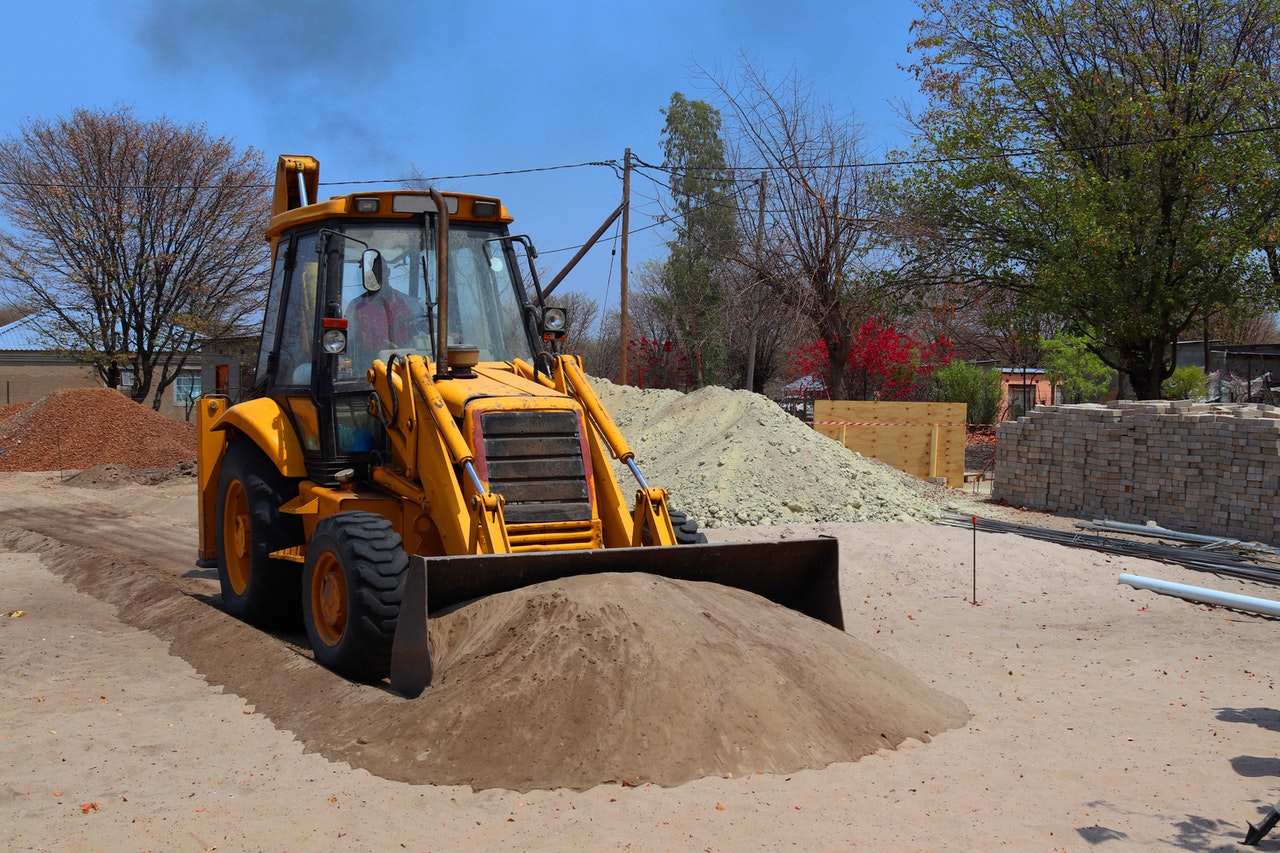
Mini pile Installations
Mini piles are installed via the same process as conventional piling, with three main stages: -Site Investigation. Before digging starts there is a requirement to do an investigation of the site conditions. This should follow the same principles as for other types of foundation work, but with extra checks for ground water and stability –
Preparation Works: The area where mini piles will be installed should be excavated down to bedrock or sub-base if there is good quality soil at that depth, depending on local conditions -Installation. The installation process requires two excavators loading their buckets with loads put on by a telescopic handler loaded with driving tubes by one worker
Noise limit values for pile-driving works are 56 dB(A) (L eq ) and 65 dB(A) (L AFmax ) depending on the time of day and location. With pile-driving activities, it is important to keep disturbance of residents to a minimum during night time hours. Pile driving operations, with or without concrete placing in situ, must be carried out between 07:00 and 18:00 hrs from Monday to Saturday -Drilling & Installation.